Home >
Production Process > Modern Improvement |
Modern Improvement |
With the development of technology, the process of rotomoulding has metamorphosed from being just a falsifiable process, relying on both trial and error and the experience of the operator, to a highly technological evolution where even the air temperature in the mold could be monitored. Much of the theoretical assumptions and hypotheses has been replaced by precise technological conformity based on microprocessors.
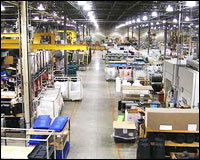
Reducing cycle time
Reducing the cycle time was the foremost aim. This new approach to faster cycles focuses mainly on alteration of the resin rather than any technological breakthrough in the mold or the machine. A leading international supplier of high performance plastics called A. Schulman has allegedly developed a new resin modification that the melt to an optimum cure in a shorter time. This Better Parts Faster (BPF) compounding technology can abridge oven cycle times up to 25% and lessen cooling times about 10%.
Mold Pressurization
The most promising area is in mold pressurization. It has been noted that if a small amount is applied internally to the mold during the heating phase, it effectuates the coalescence of the polymer particles and yields finer end products with fewer bubbles.
Temperature sensors
493K, a leading supplier of temperature and pressure measurement products for rotomolding processes from the UK has recently launched a low-cost, entry-level mold-temperature data logger called the K-Log. The device is a medium sized one-shot, one-channel temperature logger, which can be attached to the mold to collect data from one complete molding cycle. The camera sized device can later be connected to a computer to download the data so collected.
|
|
|
 |