Home > Machinery > Injection Molding Machine |
Injection Molding Machine |
Injection molding is a manufacturing process that uses both thermoplastic and thermosetting materials. In this process, a ram or screw type plunger forces plastic materials into a mold cavity, producing parts according to the contour of the mold.
Large and technically advanced machines called injection molding machines are used in this process of molding. These machines are either hydraulic powered or electrically powered. These machines, also called presses are rated by tonnage, which expresses the amount of clamping force that the machine can exert. This is the force that is responsible for keeping the mold closed during the the entire injection process. A typical injection machine consists of :
- A Hopper
- A Hydraulic Pump
- A Supporting Bed
- A Barrel fitted with a nozzle at the end
- The Mold
- Clamping Unit
- An Ejector.
As the resins are fed into the hopper, they pass through the feed throat and then enter the injection barrel, acted upon by the force of gravity. Here resins are heated to the specified melting temperature and then injected into the mold. The mold then shapes the material into the desired shape. The molds are cooled and the product is then taken out.
Usually, injection moulding machines are used to create a wide variety of plastic items from combs, car dashboards, cups, plates, bottle caps, crates, bottles and other small plastic items to larger plastic objects such as playground equipment.
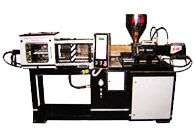
Advantages of Injection Molding Machines
Plastic injection molding machines have several advantages to offer, such as:
- Bulk production in short time
- Over 18,000 type of materials can be used
- The excess material can always be melted and reused
- These machines are completely automated and require minimal supervision.
|
|
|
 |