Home > Different Industrial Molding Processes |
Types of Plastic Molding Techniques |
The term molding encompasses, a variety of molding techniques. These technique varies in terms of the used raw polymer, moulds, tools, equipment and other accessories. Molding is the process through which different type of pvc and plastic products are manufactured using certain kinds of machines and equipments.
There are different types of plastic molding processes which are employed in molding process to produce differnt kinds of plastic products like plastic water tanks, dustbins, road barriers, storage tanks, houseware, kitchenware, and lots of other products. Some of the widely used industrial molding process are Compressions Molding, Injection Molding, Sintering, Extrusion Molding, Transfer Molding, Blow Molding, Thermoforming, Rotomolding, etc. which we have described below:
Compression Molding |
Compression molding is a high-volume, high-pressure method of molding used to produce larger flat or moderately curved parts such as hoods, fenders, scoops, spoilers, lift gates and the like for automotive end-uses. Even before plastic existed, this method was widely used in the bakery industry to mold cookies and cakes.
|
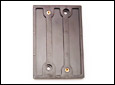 |
|
|
Injection Molding |
Injection molding is a manufacturing process that uses both thermoplastic and thermosetting materials. In this process, a ram or screw type plunger forces plastic materials into a mold cavity, producing parts according to the contour of the mold.Large and technically advanced machines called injection molding machines are used in this process of molding. |
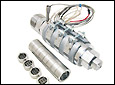 |
|
|
Sintering |
Sintering: The ISO definition of the term is:"The thermal treatment of a powder or compact at a temperature below the melting point of the main constituent, for the purpose of increasing its strength by bonding together of the particles."
|
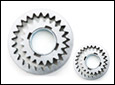 |
|
Extrusion Molding |
Extrusion molding is a type of molding process where a continuous work piece is produced by forcing molten plastic through a shaped die. This is the most used process to mass manufacture shapes with a constant cross section, like window molding, electronic enclosures, door insulation seals, pipes, rods, etc.
|
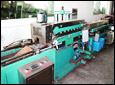 |
|
Transfer Molding |
Transfer molding is a process of molding which incorporates both injection and compression molding. Hence, the products so produced by this process Transfer Moldingpossesses good surface finish, dimensional stability, and mechanical properties typical to compression molding and the high-automation capability and low cost of injection molding.
|
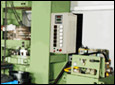 |
|
Blow Molding |
Blow molding, or blow foaming, is a novel molding process by which big hollow plastic parts like plastic beverage bottles and fuel tanks are manufactured. The process of blow molding involves melting the polymers and and forming it into a parison, which is a a plastic tube like structure with a hole in one end in which compressed air can pass through.
|
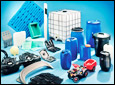 |
|
Thermoforming |
Thermoforming is a relatively simple and inexpensive manufacturing process that involves heating of plastic sheets and and transforming them into specific usable shapes. Although this process of molding was mainly used for producing food packing materials such as blister papers and disposable coffee cups , the cost andtime advantage associated with this process gradually led to its usage in a broad spectrum of industrial products.
|
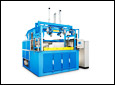 |
|
|
|